Nuclear Decommissioning
The UK and the world has an extensive ageing nuclear power fleet.
“Nuclear decommissioning is the most significant environmental challenge facing the world today, second only to climate change.” ~ Dr Michael Foster
Decommissioning nuclear sites is a complex, hazardous and expensive process.
Decommissioning is the process by which old nuclear sites are made safe. This includes the clean-up of all residual radioactivity, dismantling the structures, removing any hazardous materials or containing them for storage, and making the site safe for alternative use. It is a complex and lengthy process. The legacy nuclear fleet needs innovative, cost-effective solutions to make the decommissioning process cheaper, faster, and safer for operators.
In the UK alone, the Nuclear Decommissioning Authority’s estimated cost of decommissioning and clean-up is around £131 billion and they predict the process could take up to 120 years. Of the UK’s 19 sites, Sellafield is the largest and has the most diverse range of nuclear-based activities in Europe. It, therefore, presents the most significant and complex challenge of all the nuclear sites.
i3D is designing
bespoke vision systems
i3D robotics is working with partners to develop systems to aid nuclear decommissioning. It is part of the Nuclear Decommissioning Authority team led by Jacobs to develop 3D mapping technology using stereo vision. i3D is also conducting further work with the National Nuclear Laboratory (NNL), UKAEA, and Game Changers.
Funding for this work has been granted by Innovate UK with the UKRI and Sellafield and managed by FIS360 and the NNL.
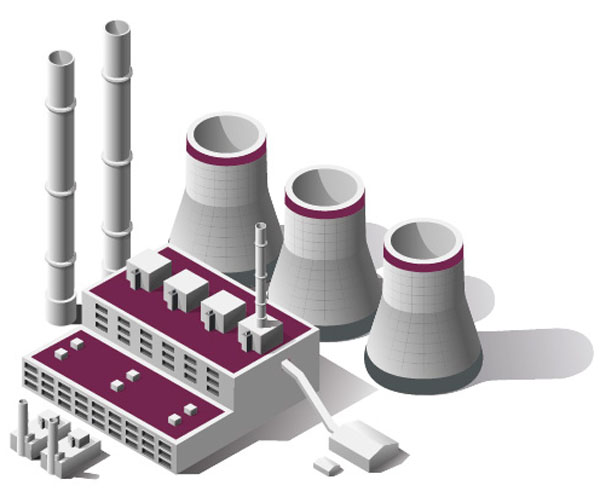
i3D is helping to make nuclear decommissioning a faster, less expensive process and making it safer for human operators.
We are designing and producing bespoke stereo vision cameras and housings to meet the challenges specific to nuclear decommissioning.
The cameras are combined machine learning algorithms and artificial intelligence to map the terrain of unknown environments and identify their contents. These integrated systems can be mounted on robots to be deployed remotely allowing unknown environments to be mapped comprehensively, more quickly than by previous methods of observation and investigation, and with minimum risk to human operators.
- 3D mapping software creates comprehensive replication of an environment in almost real-time
- Machine learning algorithms enable the identification of potentially hazardous objects
- Hardware is small and light enough to be mounted on a robot and manoeuvred around cluttered constrained environments
- Stereo vision cameras are radiation resistant
- Robotic mounting allows for remote deployment
- Tailored solutions for unprecedented levels of resolution and accuracy
- Can be combined with a Raman spectrometer to provide characterisation of unknown substances
- Modular design allows for incorporation of other technologies such as virtual reality, thermal imaging or radiation sensors