Ceramics – Bricks, Tiles, & Sanitaryware
‘Modern’ brickmaking methods date from Tudor times!
The Romans brought brickmaking to Britain, and it’s been a key component of the Construction industry ever since. Clay bricks and roof tiles are weather and damp-resistant, can withstand a range of temperatures and require little maintenance. The brickmaking process has remained unchanged: ground clay is mixed with water, which is then formed into the desired shape. These are then dried and fired.
Since Tudor times, kilns have been used for baking bricks and roof tiles. They are placed on a conveyer belt system (kiln cars) and moving them through a tunnel kiln. These are between 100 and 200 metres long, up to 3 metres high and are heated to between 900–1200 °C.
During firing, the minerals in the clay, particularly iron oxide, give colour to the brick as they absorb oxygen. This is where bricks get their red colour.
Not all bricks come through the process to pass inspection. To be of saleable standard for use in Construction, bricks must conform to a particular shade within set tolerances, display colour variance through a set area, and be free from defects and cracks of a size which could cause the brick to fail or that is unsightly. Human operators make inspections by eye, increasing the possibility of missed defects and greater colour variation. Up to 30% of all bricks manufactured fail these standards and are discarded, crushed and sent to lesser purposes.
We are heading an Innovate UK-funded project where, with partners, our stereo-vision camera systems are being tested in real-world conditions for brick and roof tile quality inspection monitoring with excellent results.

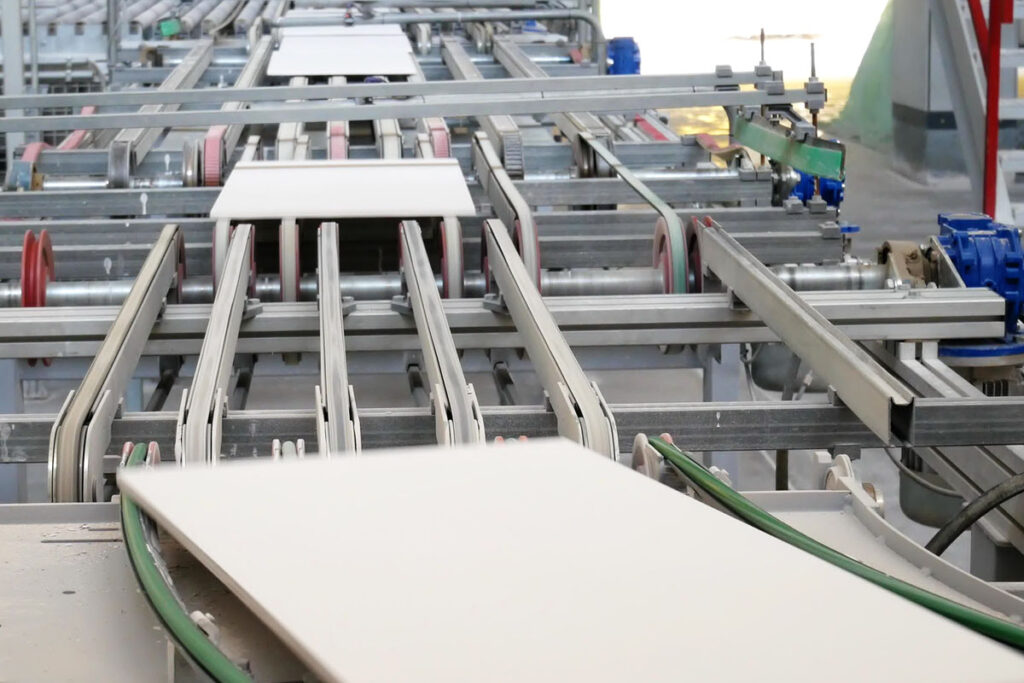
The demand for bathroom sanitaryware continues to grow, yet little of the manufacturing process has changed since the Industrial Revolution.
With an ever-increasing demand for housing, the need for bathroom sanitaryware is rising. As with Steel and Glass, the Ceramics sector requires innovative technologies to cut waste and costs to remain competitive and carbon emissions to avoid penalties for missed net zero-linked targets.
Ceramics are moulded into the required product and then fired in hot ovens to set them. Impurities in slip composition or weak spots incorporated during the moulding of the products can result in catastrophic failure of the product when heated.
i3Dr is leveraging the technologies used in defect detection for Glass and Steel and adapting them to the Ceramics sector. The versatile nature of our stereo imaging systems means they can be incorporated with other sensors and instruments. For example, we are working with a partner company, IS-Instruments, on using Raman spectroscopy to monitor the homogeneity of slip composition.