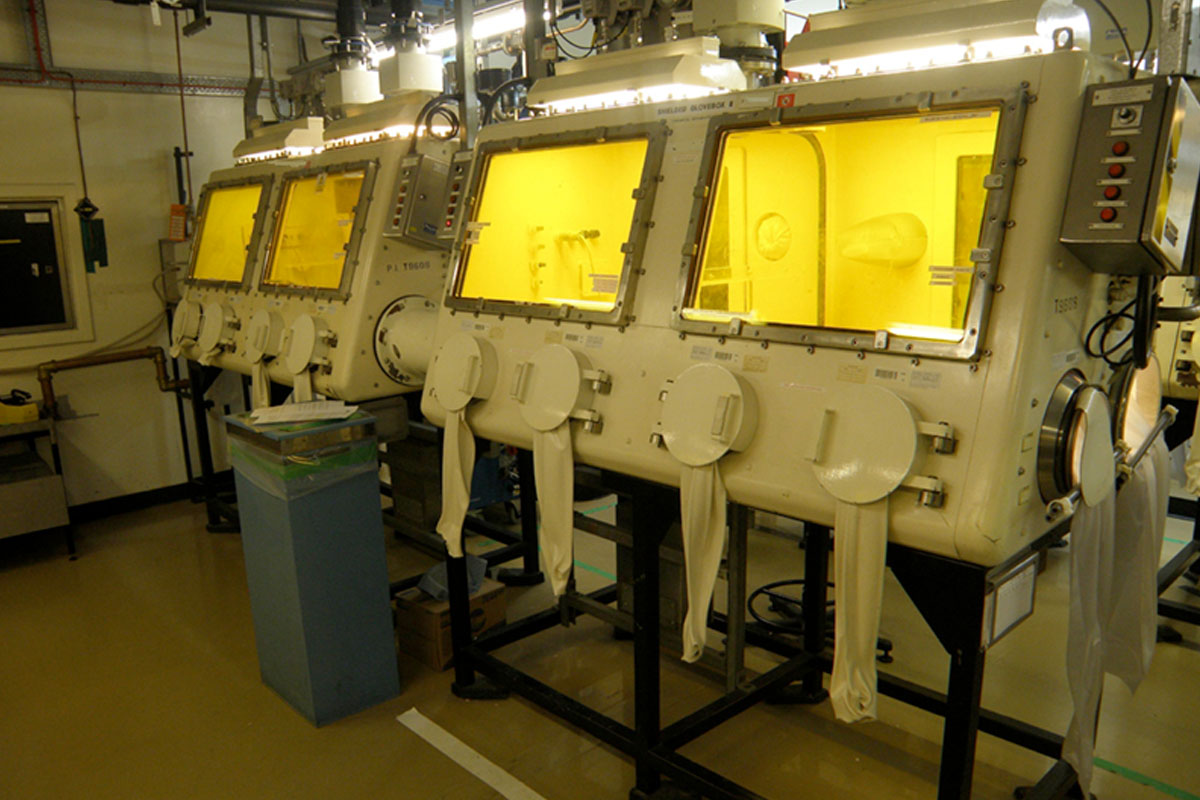
The Sellafield nuclear facility in Cumbria presents the largest and most intricate decommissioning challenge of our time.
Home to the UK’s first-generation nuclear reactors, the site was the focus of plutonium production for nuclear weapons, the first industrial-scale nuclear power station in the UK, and its current function as a waste site facility and centre of reprocessing for spent nuclear fuel. It is also where the National Nuclear Laboratory (NNL) has its central laboratory and Headquarters. Based over two square miles, Sellafield is not only Europe’s largest nuclear site, but it also has the most diverse range of nuclear facilities anywhere in the world.
Decommissioning nuclear sites is time-consuming, costly, and inherently dangerous for humans. As a result, technologies need to be developed to speed up the process, bring down costs, and reduce risk. In 2018, Game Changers, an innovation programme delivered by the NNL and FIS360, launched a challenge related to gloveboxes at Sellafield.
Historically used for research, development and fuel fabrication operations, there are around 350 gloveboxes on site ranging in size from around one cubic metre up to several cubic metres. At 60 years old, they exist in various states of disrepair and with little to indicate conditions inside. Until this point, determination of contents had been achieved by inserting an endoscope through the access ports. However, a more sophisticated approach was required to ensure hazards were not misidentified or overlooked.
The Glovebox Challenge:
350 gloveboxes, contents unknown, sealed, ventilated, held under depression in an inert atmosphere
- Accessible via entry ports ranging from 6 inches up to 20 inches with the average at 10 inches. Sensor system would need to fit into the glovebox via these posting ports and be small enough to access all areas inside
- Gloveboxes many contain pipework, vessels, cabling, valves, and furnaces which must be negotiated around
- Sensors should provide real-time images with object recognition alerting operators to the presence of potentially sharp objects
- Sharp objects could be constructed of a variety of materials: magnetic and non-magnetic metals, glass, plastic, rubber, or ceramic
- Viewing windows (glass or polymer-based such as Perspex) may have degraded to the point of opacity and there may be radiation shielding on the outside of some gloveboxes further reducing visibility and making a determination of contents difficult or impossible
- Some gloveboxes do not have power or lighting
- Equipment may need to be resistant to the effects of radiation
“The challenge, as we could see it, was several-fold. Not only are the gloveboxes up to 60 years old, but there is limited documentation of their contents.
Many of the viewing windows have degraded over time, so visibility is poor to non-existent. The contents of the gloveboxes are, therefore, not easily identifiable, and there is potential for hazardous and sharp objects to result in harmful exposure to Glovebox operators. This project focuses specifically on the identification of sharp objects. i3D has been developing object recognition and AI-related technologies for years. Our stereo vision algorithms, originally developed for the Mars Rovers missions, have proven robust, are accurate and produce real time representations. We are already engaged in the nuclear industry working in infrastructure, object recognition and location, so this was a natural extension of that work.” – Nicholas Bantin, Director, i3D robotics
i3D was invited to Sellafield to discuss the submission of the successful application, and the challenge went ahead.
Dr Benjamin Crutchley, Senior Machine Vision Engineer at i3D, said
“Through coupling object detection algorithms with our stereo vision algorithms we can detect sharp or hazardous objects as well as aiding glovebox operators in viewing the contents of the gloveboxes through 2D images or 3D models. The operators can effectively navigate a scene like a CAD model. The development also uses machine learning algorithms to perform object detection. This allows for the upscaling of the technology as additional objects may be added later or for the models to be retrained if required.”
Watch out for part 2 of this blog, in which we describe how the technology works.